Analyzing Thermal Processes in Laser Welding of Multi- Component Heat-Resistant Alloy Thin-Walled Butt Joints: A Comprehensive Modeling Approach
DOI:
https://doi.org/10.12928/si.v21i2.151Keywords:
Laser welding, thin-walled parts, butt joints, multi-component heat-resistant alloysAbstract
Niobium-based alloys are vital in high-temperature environments due to their unique chemical composition, phase structure, high density, and oxidation resistance. These alloys find extensive applications in industries such as medicine, engine manufacturing, and space technology. This study delves into the complexities of modeling laser welding processes, necessitated by the multitude of dynamic parameters specific to each surface configuration. Finite element modeling was conducted using COMSOL Multiphysics to analyze the heat transfer in butt joints between Nb-15W-5Mo-1Zr alloy plates under 400 W laser radiation power. The research employed finite element modeling to analyze heat transfer in Nb-15W-5Mo-1Zr alloy plates, considering non-uniform movement at the start and end of the welding process, Gaussian heat flux distribution along the laser spot radius, and temperature-dependent reflection coefficient. The models accounted for non-uniform movement, Gaussian heat flux distribution, and temperature-dependent reflection coefficient. The study demonstrated that thin plates of Nb-15W-5Mo-1Zr alloy can be effectively welded using specific laser processing modes, leveraging their high initial cooling rate of 1.2-1.3 s. Successful welding of Nb-15W-5Mo-1Zr alloy plates requires careful consideration of laser processing parameters. While the alloy's thermodynamic properties allow for effective welding, ensuring weld quality mandates additional production processes aimed at preventing potential part failure.
References
F. Heisterkamp and T. Carneiro, “Niobium, Science & Technology 2001,” in Niobium, Science & Technology: Proceedings of the International Symposium Niobium 2001, pp. 1109–1160.
C. C. Wojcik, “Processing, properties and applications of high-temperature niobium alloys,” MRS Proceedings, vol. 322, 1993. doi:10.1557/proc-322-519.
Y.-H. Hon, J.-Y. Wang, and Y.-N. Pan, “Composition/phase structure and properties of titanium-niobium alloys,” MATERIALS TRANSACTIONS, vol. 44, no. 11, pp. 2384–2390, 2003. doi:10.2320/matertrans.44.2384
Y. Zhang, Q. Wei, P. Xie, and X. Xu, “An ultrastrong niobium alloy enabled by refractory carbide and eutectic structure,” Materials Research Letters, vol. 11, no. 3, pp. 169–178, 2022. doi:10.1080/21663831.2022.2133977
R. Tanaka et al., “Newly developed niobium-based superalloys for elevated temperature application” in “Niobium for High Temperature Applications” 2004 TMS 133rd Annual Meeting and Exhibition, 2004.
I. Chou, D. A. Koss, P. R. Howell, and A. S. Ramani, “High-temperature deformation of a mechanically alloyed niobium-yttria alloy,” Materials Science and Engineering: A, vol. 222, no. 1, pp. 14–20, 1997. doi:10.1016/s0921-5093(96)10450-0
L. D. Zardiackas, M. J. Kraay, and H. L. Freese, Titanium, Niobium, Zirconium, and Tantalum for Medical and Surgical Applications. West Conshohocken, PA: ASTM, 2006.
J. Xu et al., “Potential use of porous titanium–niobium alloy in orthopedic implants: Preparation and experimental study of its biocompatibility in vitro,” PLoS ONE, vol. 8, no. 11, 2013. doi:10.1371/journal.pone.0079289
C. Stechman, P. Woll, R. Fuller, and A. Colette, “A high performance liquid rocket engine for satellite main propulsion,” 36th AIAA/ASME/SAE/ASEE Joint Propulsion Conference and Exhibit, 2000. doi:10.2514/6.2000-3161
C. Liu, J. Chen, H. Han, Y. Wang, and Z. Zhang, “A long duration and high reliability liquid apogee engine for satellites,” Acta Astronautica, vol. 55, no. 3–9, pp. 401–408, 2004. doi:10.1016/j.actaastro.2004.05.030
M. F. Diaz-Aguado et al., “Experimental investigation of total photoemission yield from new satellite surface materials,” Journal of Spacecraft and Rockets, vol. 56, no. 1, pp. 248–258, 2019. doi:10.2514/1.a34245
B. Vishwanadh, N. N. Kumar, G. Samyuktha, V. Kaushik, and R. Tewari, “Development of a new thermo-mechanical processing route for NB-5MO-1Zr-0.1c (wt%) alloy,” Journal of Alloys and Compounds, vol. 942, p. 168860, 2023. doi:10.1016/j.jallcom.2023.168860
E. A. Loria, “Niobium-base superalloys via Powder Metallurgy Technology,” JOM, vol. 39, no. 7, pp. 22–26, 1987. doi:10.1007/bf03258035
M. Ali and S. K. Vadali, “Development of electron beam welding procedure for NB-1Zr-0.1C alloy,” Materials Today: Proceedings, vol. 3, no. 9, pp. 2913–2919, 2016. doi:10.1016/j.matpr.2016.09.003
J. Yang, Y. Huang, B. Liu, C. Guo, and J. Sun, “Precipitation behavior in a Nb-5W-2Mo-1Zr niobium alloy fabricated by electron beam selective melting,” Materials Characterization, vol. 174, p. 111019, 2021. doi:10.1016/j.matchar.2021.111019
M. M. Quazi et al., “Current research and development status of dissimilar materials laser welding of titanium and its alloys,” Optics & Laser Technology, vol. 126, p. 106090, 2020. doi:10.1016/j.optlastec.2020.106090
V. D. Shelyagin, A. V. Bernatsky, O. V. Siora, V. I. Bondareva and M. P. Brodnikovskyi, “Structure of laser welded joints of multicomponent high-entropy alloy of Nb–Cr–Ti–Al–Zr system,” The Paton Welding Journal, no. 6, pp. 26-31, 2021. doi: 10.37434/tpwj2021.06.04
A. Bernatskyi, V. Lukashenko, O. Siora, M. Sokolovskyi, N. Shamsutdinova, “Determination of the influence of laser welding parameters on the weld quality assurance of heat-resistant alloys,” International Journal for Research in Applied Science and Engineering Technology (IJRASET), vol. 9, no. XII, pp. 612-615, 2021. doi: 10.22214/ijraset.2021.39313
R. Fabbro and K. Chouf, “Keyhole modeling during laser welding,” Journal of Applied Physics, vol. 87, no. 9, pp. 4075–4083, 2000. doi:10.1063/1.373033
M. J. Torkamany, F. Malek Ghaini, and R. Poursalehi, “An insight to the mechanism of weld penetration in dissimilar pulsed laser welding of Niobium and Ti–6Al–4V,” Optics & Laser Technology, vol. 79, pp. 100–107, 2016. doi:10.1016/j.optlastec.2015.11.005
M. J. Torkamany, F. Malek Ghaini, R. Poursalehi, and A. F. H. Kaplan, “Combination of laser keyhole and conduction welding: Dissimilar laser welding of niobium and Ti-6Al-4V,” Optics and Lasers in Engineering, vol. 79, pp. 9–15, 2016. doi:10.1016/j.optlaseng.2015.11.001
M. J. Torkamany, F. Malek Ghaini, and R. Poursalehi, “Dissimilar pulsed Nd:YAG laser welding of pure niobium to Ti–6Al–4V,” Materials & Design, vol. 53, pp. 915–920, 2014. doi:10.1016/j.matdes.2013.07.094
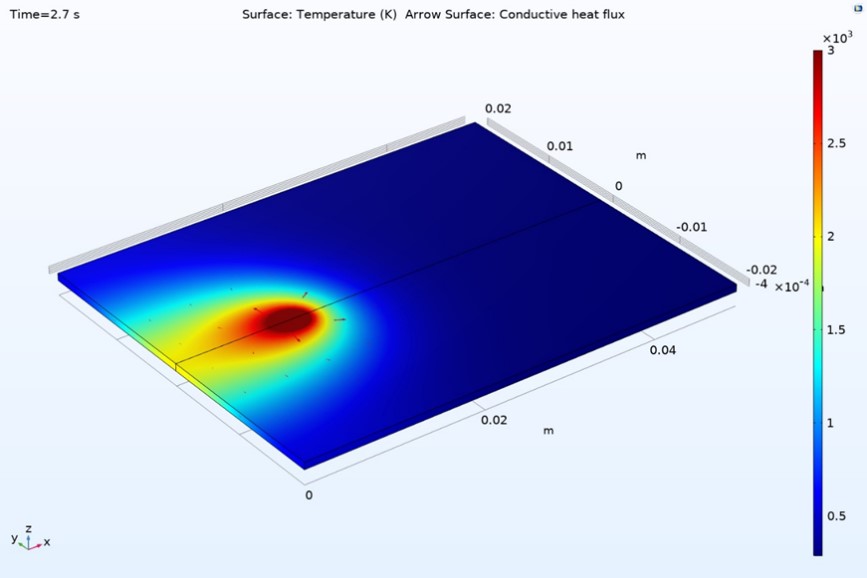
Downloads
Published
How to Cite
Issue
Section
License
Copyright (c) 2023 Mykola Sokolovskyi, Artemii Bernatskyi, Oleksandr Siora, Valentyna Bondarieva, Yurii Yurchenko, Nataliia Shamsutdinova, Oleksandr Danyleiko

This work is licensed under a Creative Commons Attribution-ShareAlike 4.0 International License.