Design and Integration of a Robotic Welding Parameterized Procedure for Industrial Applications
DOI:
https://doi.org/10.12928/si.v22i1.179Keywords:
Sensor, Controller, Actuators, RobotAbstract
This paper explores the development of an effective motion planning strategy for robotics welding in tube to tubesheet joints, a critical process in heat exchanger manufacturing. The research methodology follows an experimental paradigm, investigating two distinct approaches to tackle the intricacies of this task. The initial approach, involving a welding torch affixed to the robotic arm's flange, proved ineffective due to the complexity of continuous 360° orbital welding. This led to the adoption of a custom end effector in the second approach, designed to enhance adaptability and precision. Key tools and materials employed in this research include the Robot Operating System (ROS), Rviz for 3D visualization, MoveIt for motion planning, SolidWorks for CAD modelling, and the xArm7 Robotic Arm. These tools facilitated the creation of a comprehensive planning environment. The motion planning process relies on three essential parameters: tube diameter, type of tube to tubesheet joint (flush or protruding), and the 3D coordinates of tube centers. A Python scripts control the robot's movements, with specific joint state and pose goals for precise positioning. Finally, this study contributes to present a program that orchestrates the robotic arm's motion, simulating the welding process for tube to tubesheet joints. This comprehensive research endeavor contributes to the optimization of motion planning strategies in the context of tube to tubesheet welding, with practical applications in the manufacturing industry.
References
American Society of Mechanical Engineers (ASME), (2015). ASME Boiler and Pressure Vessel Code, Section 8, Division 1: Rules for Construction of Pressure Vessels, p136.
Arregi, M. O., & Secco, E. L. (2023). Operative Guide for 4-wheel Summit XL Mobile Robot Set-up. Acta Scientific Computer Sciences,5(4), https://core.ac.uk/download/pdf/559427479.pdf.
Brawner, S. (2021). sw_urdf_exporter, ROS Wiki, http://wiki.ros.org/sw_urdf_exporter.
Daniel, W. (2021). The difference between UFACTORY xArm5, UFACTORY xArm6 and UFACTORY xArm7 | UFACTORY Help Center, http://help.ufactory.cc/en/articles/4491842-the-difference-between-ufactory-xarm5-ufactory-xarm6-and-ufactory-xarm7.
Dongming, W., Zengfu, G., Li, T. and Feng, T. (1995). The technical summary of tube-sheet welding of heat-exchangers in China and out of China. Press Vessel Technol, 12, 48–53.
Er, B.H. and Das, T. (2023). Comparison of Orbital and Manual Welding for Manufacturing Stainless Steel Heat Exchanger. International Journal of Advanced Natural Sciences and Engineering Researches, 7(6), 358–362, doi: https://doi.org/10.59287/ijanser.1173.
Eren, B., Demir, M.H. and Mistikoglu, S. (2023). Recent developments in computer vision and artificial intelligence aided intelligent robotic welding applications. The International Journal of Advanced Manufacturing Technology, 126(11), 4763–4809, doi: https://doi.org/10.1007/s00170023114564.
Gao, W., Tang, Q., Yao, J. and Yang, Y. (2020). Automatic motion planning for complex welding problems by considering angular redundancy. Robotics and Computer-Integrated Manufacturing, 62, 101862, doi: https://doi.org/10.1016/j.rcim.2019.101862.
Ge, Y., Xu, Y., Yu, H., Chen, C., & Chen, S. (2019). A method for detecting central coordinates of girth welds based on inverse compositional AAM in tube-tube sheet welding. In Transactions on Intelligent Welding Manufacturing: Volume II No. 3 2018 (pp. 65-81), Springer Singapore, https://doi.org/10.1007/978-981-13-7418-0_4.
Haldankar, T., Kedia, S., Panchmatia, R., Parmar, D., & Sawant, D. (2022, February). Design of robotic manipulator for welding using ROS and Gazebo. In 2022 IEEE Delhi Section Conference (DELCON) (pp. 1-6), IEEE, doi: https://doi.org/10.1109/DELCON54057.2022.9753305.
Hernandez-Mendez, S., Maldonado-Mendez, C., Marin-Hernandez, A., Rios-Figueroa, H. V., Vazquez-Leal, H., & Palacios-Hernandez, E. R. (2017, November). Design and implementation of a robotic arm using ROS and MoveIt!. In 2017 IEEE International Autumn Meeting on Power, Electronics and Computing (ROPEC) (pp. 1-6), IEEE, doi: https://doi.org/10.1109/ROPEC.2017.8261666.
Hershberger, D. (2019). rviz - ROS Wiki, http://wiki.ros.org/rviz.
Joseph, L., & Cacace, J. (2018). Mastering ROS for Robotics Programming: Design, build, and simulate complex robots using the Robot Operating System, Packt Publishing Ltd.
Pitonakova, L., Giuliani, M., Pipe, A., & Winfield, A. (2018). Feature and performance comparison of the V-REP, Gazebo and ARGoS robot simulators. In Towards Autonomous Robotic Systems: 19th Annual Conference, TAROS 2018, Proceedings 19 (pp. 357-368), Springer International Publishing, doi: https://doi.org/10.1007/978-3-319-96728-8_30.
Linquip, T. (2021). Heat Exchanger Parts: The Advantages of Each Component, Linquip, https://www.linquip.com/blog/heat-exchanger-parts-a-complete-description/.
Lumelsky, V. L. A. D. I. M. I. R. J. (1987). Effect of kinematics on motion planning for planar robot arms moving amidst unknown obstacles, IEEE Journal on Robotics and Automation, 3(3), 207-223, doi: https://doi.org/10.1109/JRA.1987.1087094.
Manolescu, V. D., & Secco, E. L. (2022, August). Design of an assistive low-cost 6 dof robotic arm with gripper. In Proceedings of Seventh International Congress on Information and Communication Technology: ICICT 2022, London, Volume 1 (pp. 39-55), Singapore: Springer Nature Singapore, doi: https://doi.org/10.1007/978-981-19-1607-6_4.
Open Robotics. (2022). Gazebo, https://gazebosim.org/about.
Ren, K., Lu, Z., Dong, H., Cheng, D., Yu, Y., Cui, R., ... & Yan, S. (2018, August). Target Grasping and Obstacle Avoidance Motion Planning of Humanoid Robot. In 2018 IEEE International Conference on Intelligence and Safety for Robotics (ISR) (pp. 250-255), IEEE, doi: https://doi.org/10.1109/IISR.2018.8535650.
Sears-Collins, A. (2021). What is the Difference Between rviz and Gazebo? – Automatic Addison, https://automaticaddison.com/what-is-the-difference-between-rviz-and-gazebo/.
Tellez, R. (2018). What is moveit_ros? All about Movelt! ROS, The Construct, https://www.theconstructsim.com/ros-movelt/.
Tharmalingam, K., & Secco, E. L. (2023, April). A Surveillance Mobile Robot Based on Low-Cost Embedded Computers. In Proceedings of 3rd International Conference on Artificial Intelligence: Advances and Applications: ICAIAA 2022 (pp. 323-334), Singapore: Springer Nature Singapore, https://doi.org/10.1007/978-981-19-7041-2_25.
Thekkuden, D. T., Mourad, A. H. I., & Bouzid, A. H. (2021). Failures and leak inspection techniques of tube-to-tubesheet joints: a review, Engineering Failure Analysis, 130, 105798, https://doi.org/10.1016/j.engfailanal.2021.105798.
Sucan, I. A., Moll, M., & Kavraki, L. E. (2012). The open motion planning library, IEEE Robotics & Automation Magazine, 19(4), 72-82, https://doi.org/10.1109/MRA.2012.2205651.
UFACTORY (2023). Contents, GitHub, https://github.com/xArm-Developer/xarm_ros.
Waldron, S.R. (2020). Secrets to a Lasting Tube to tubesheet Joint: Properly Pre-Setting Tubes, HydroPro, https://www.hpro.com/post/secrets-to-a-lasting-tube-to-tubesheet-joint-properly-pre-setting-tubes.
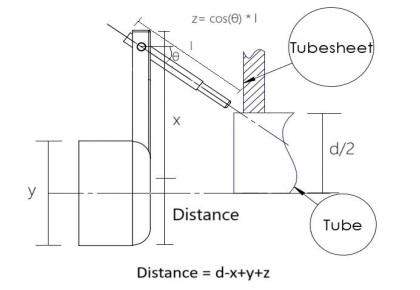
Downloads
Published
How to Cite
Issue
Section
License
Copyright (c) 2024 Sangeeth Puthussery, Emanuele Lindo Secco

This work is licensed under a Creative Commons Attribution-ShareAlike 4.0 International License.