Enhancing Pharma Manufacturing Efficiency: Integrating Lean Six Sigma and Fuzzy FMEA for Waste Reduction
DOI:
https://doi.org/10.12928/si.v22i2.199Keywords:
Lean Manufacturing, Six Sigma, Lean Six Sigma, Fuzzy FMEA, Production ProcessAbstract
In pharmaceutical manufacturing, inefficiencies such as waiting times, excessive material usage, and packaging defects can significantly impact productivity and quality. This study adopts a Lean Six Sigma approach, integrating lean manufacturing and six sigma methodologies, to systematically address these challenges. Through Process Activity Mapping (PAM), it was determined that value-added (VA) activities account for approximately 63% of total production activities, while non-value-added (NVA) and essential non-value-added (ENVA) activities contribute about 34% and 4%, respectively. Critical waste was identified using the genba shikumi method, followed by Failure Modes and Effects Analysis (FMEA) to determine Risk Priority Numbers (RPNs). Fuzzy logic was applied to prioritize the suggested improvements for more accurate risk assessments. Key recommendations based on Fuzzy RPN rank include, enhancing bulk product quality before printing, implementing rigorous inspections of the printing process, optimizing machine utilization, and adjusting production schedules using the Shortest Processing Time (SPT) method.
References
Badan Pusat Statistik. (2021). Economic Indicators; Badan Pusat Statistik: Central Jakarta, Indonesia.
Belekoukias, I., Garza-Reyes, J. A., & Kumar, V. (2014). The impact of lean methods and tools on the operational performance of manufacturing organisations. International Journal of production research, 52(18), 5346-5366, https://doi.org/10.1080/00207543.2014.903348.
Boral, S., Howard, I., Chaturvedi, S. K., McKee, K., & Naikan, V. N. A. (2020). An integrated approach for fuzzy failure modes and effects analysis using fuzzy AHP and fuzzy MAIRCA. Engineering Failure Analysis, 108, 104195, https://doi.org/10.1016/j.engfailanal.2019.104195.
Bowles, J. B., & Peláez, C. E. (1995). Fuzzy logic prioritization of failures in a system failure mode, effects and criticality analysis. Reliability engineering & system safety, 50(2), 203-213,
https://doi.org/10.1016/0951-8320(95)00068-D.
Braglia, M., Frosolini, M., & Montanari, R. (2003). Fuzzy TOPSIS approach for failure mode, effects and criticality analysis. Quality and reliability engineering international, 19(5), 425-443,
https://doi.org/10.1002/qre.528.
Catelani, M., Ciani, L., & Venzi, M. (2018). Failure modes, mechanisms and effect analysis on temperature redundant sensor stage. Reliability Engineering & System Safety, 180, 425-433,
https://doi.org/10.1016/j.ress.2018.08.013.
Catelani, M., Ciani, L., & Venzi, M. (2018). Failure modes, mechanisms and effect analysis on temperature redundant sensor stage. Reliability Engineering & System Safety, 180, 425-433,
https://doi.org/10.1016/j.ress.2018.08.013.
Deif, A. M., & ElMaraghy, H. (2014). Cost performance dynamics in lean production leveling. Journal of Manufacturing Systems, 33(4), 613-623, https://doi.org/10.1016/j.jmsy.2014.05.010.
Ellianto, M. S., Santoso, P. B., & Sonief, A. A. (2015). Proposal for the Implementation of Lean Six Sigma, FMEA, and Fuzzy to Improve the Quality of Liquid Soap Bottle Products. JEMIS, VOL 3 NO 1.
Hasanah, T. U., Wulansari, T., Putra, T., & Fauzi, M. (2020). Implementation of Lean Manufacturing with Takt Time and FMEA Methods to Identify Waste in Sterile Production Processes in the Pharmaceutical Industry. Journal of Systems Engineering and Industry, Volume 07, No. 02.
Huang, G., Xiao, L., & Zhang, G. (2020). Improved failure mode and effect analysis with interval-valued intuitionistic fuzzy rough number theory. Engineering Applications of Artificial Intelligence, 95, 103856, https://doi.org/10.1016/j.engappai.2020.103856.
Huang, G., Xiao, L., & Zhang, G. (2020). Improved failure mode and effect analysis with interval-valued intuitionistic fuzzy rough number theory. Engineering Applications of Artificial Intelligence, 95, 103856, https://doi.org/10.1016/j.engappai.2020.103856.
Jilcha, K., & Kitaw, D. (2015). Lean philosophy for global competitiveness in Ethiopia chemical industries: Review. Journal of Computer Science and Systems Biology, 8(6), 304-321,
https://doi.org/10.4172/jcsb.1000205.
Kumru, M., & Kumru, P. Y. (2013). Fuzzy FMEA application to improve purchasing process in a public hospital. Applied soft computing, 13(1), 721-733, https://doi.org/10.1016/j.asoc.2012.08.007.
Lakshmi, R., & Baskar, S. (2019). Novel term weighting schemes for document representation based on ranking of terms and Fuzzy logic with semantic relationship of terms. Expert Systems with Applications, 137, 493-503, https://doi.org/10.1016/j.eswa.2019.07.022.
Liu, H. C., Li, Z., Song, W., & Su, Q. (2017). Failure mode and effect analysis using cloud model theory and PROMETHEE method. IEEE Transactions on Reliability, 66(4), 1058-1072,
https://doi.org/10.1109/TR.2017.2754642.
Liu, H. C., Liu, L., & Liu, N. (2013). Risk evaluation approaches in failure mode and effects analysis: A literature review. Expert systems with applications, 40(2), 828-838,
https://doi.org/10.1016/j.eswa.2012.08.010.
Liu, H. C., Wang, L. E., Li, Z., & Hu, Y. P. (2018). Improving risk evaluation in FMEA with cloud model and hierarchical TOPSIS method. IEEE Transactions on Fuzzy Systems, 27(1), 84-95,
https://doi.org/10.1109/TFUZZ.2018.2861719.
Lo, H. W., Liou, J. J., Huang, C. N., & Chuang, Y. C. (2019). A novel failure mode and effect analysis model for machine tool risk analysis. Reliability Engineering & System Safety, 183, 173-183, https://doi.org/10.1016/j.ress.2018.11.018.
Ministry of Health RI. (2020). Action Plan Program 2020-2024”. Jakarta: Health Research and Development Agency, Ministry of Health, Republic of Indonesia.
Mwacharo, F. K. (2013). Challenges of Lean Management: Investigating the challenges and developing a recommendation for Lean Management.
Nilay Yucenur, G., Cataltepe, S., & Sakin, I. (2020). An integrated approach by fmea & fuzzy prioritization method at pharmaceutical industry quality control. Cumhuriyet Science Journal, 41(1), 106-121, https://doi.org/10.17776/csj.567601.
Panchal, D., Singh, A. K., Chatterjee, P., Zavadskas, E. K., & Keshavarz-Ghorabaee, M. (2019). A new fuzzy methodology-based structured framework for RAM and risk analysis. Applied Soft Computing, 74, 242-254, https://doi.org/10.1016/j.asoc.2018.10.033.
Rahman, A., Setyanto, N. W., & Syahindri, P. K. (2010). Lean Sigma Approach as Effort to Minimize Waste in Pharmaceutical Packaging Processes. Proceedings of the Fourth National Seminar on Management & Quality Engineering.
Silva, M. M., de Gusmão, A. P. H., Poleto, T., e Silva, L. C., & Costa, A. P. C. S. (2014). A multidimensional approach to information security risk management using FMEA and fuzzy theory. International Journal of Information Management, 34(6), 733-740, https://doi.org/10.1016/j.ijinfomgt.2014.07.005.
Sun, Liu, & Zhang. (2019). A fuzzy-AHP-based FMEA approach for mobile vehicle tracking systems. Soft Computing. 1847-186.
Wang, Y. M., Chin, K. S., Poon, G. K. K., & Yang, J. B. (2009). Risk evaluation in failure mode and effects analysis using fuzzy weighted geometric mean. Expert systems with applications, 36(2), 1195-1207, https://doi.org/10.1016/j.eswa.2007.11.028.
Wang, Z., Gao, J. M., Wang, R. X., Chen, K., Gao, Z. Y., & Zheng, W. (2017). Failure mode and effects analysis by using the house of reliability-based rough VIKOR approach. IEEE Transactions on Reliability, 67(1), 230-248, https://doi.org/10.1109/TR.2017.2778316.
Xiao, N., Huang, H. Z., Li, Y., He, L., & Jin, T. (2011). Multiple failure modes analysis and weighted risk priority number evaluation in FMEA. Engineering Failure Analysis, 18(4), 1162-1170, https://doi.org/10.1016/j.engfailanal.2011.02.004.
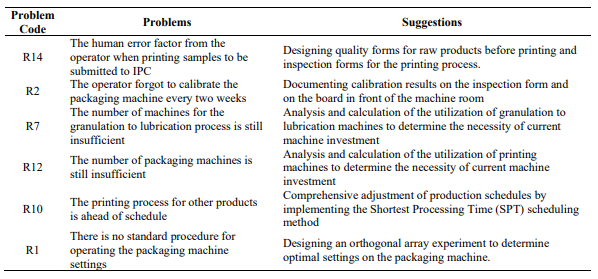
Downloads
Published
How to Cite
Issue
Section
License
Copyright (c) 2024 Rindi Kusumawardani

This work is licensed under a Creative Commons Attribution-ShareAlike 4.0 International License.